Your opinion on the - somewhat technical and diffficult to describe issue below - is much appreaciated!
Interesting, though somewhat annoying difference between the M35B parts manual and the ‘as-built’ engine, installed in my C36MkII. It surfaced because it became increasingly difficult to keep the ‘fan belt’ properly tensioned, causing excessive belt wear.
See sketch below....
According to the M35B Parts Manual, the alternator is fixed onto a bracket (3), allowing it to slide along it, to tension the belt (9) and fix it in proper position with an M8 bolt (5) and two washers (6)(7). Seems sensible and common way to install an alternator.
Now… on the other side, the bracket (3) should be fixed with two M6 bolts (1)(8), through two holes in the bracket and two spacers (4). Bolts (1) & (8) are screwed into threaded holes in the (aluminum) Thermostat housing. Personally I would have preferred threaded rod and nuts in this application, but at least the design allows for some torque and fixes the bracket (3) in position. See yellow lines on sketch.
[IMG]http://www.c36ia.com/forums/attachment.php?attachmentid=1395&stc=1&d=137...
On my engine however (see picture), the bracket (3) has only one hole; the bottom hole only. The bracket (3) is mounted to the thermostat using the top bolt (1) only. To prevent rotation of the bracket - due to the alternator torque and vibrations – bolt (1) needs extreme tightening.
And even then, belt slip is difficult to prevent. Note that black dust from belt wear! :eek:
Given the fact the bracket (3) only has one hole, I presume the engine was delivered by OEM this way...
[IMG]http://www.c36ia.com/forums/attachment.php?attachmentid=1396&stc=1&d=137...
What’s worse the the aluminium threading in the thermostat housing isn’t up to the required tensioning of bolt (1); the threads yield and become unusable. I tapped 8 mm threads into the thermostat to replacing the original 6 mm threading. *) Instead of bolt (1), I used threaded rod (stud) and a nut. I would’ve upgraded to 10 mm if I could, but there’s no room in the thermostat for that.
I consider to drill a second hole into bracket (3) and use bolt (8) as a second fixation point for it. However I’m not yet sure the current bolt (8) in the thermostat (see close up in picture) is long enough; it also fixes the thermostat to the engine itself. And… is the bracket long enough with sufficient room for belt replacement/tension adjustment?
And... not before I know what the construction is like on other M35B engines...
Afterthought! Why is this metric while most other engine parts - even bolt (5) on the alternator - are imperial units?! :confused:
*) If anybody needs info on threading and required tools; say so!
S/Y 'EASY'
C36 MkII #1739
Monnickendam -The Netherlands
www.taas.it
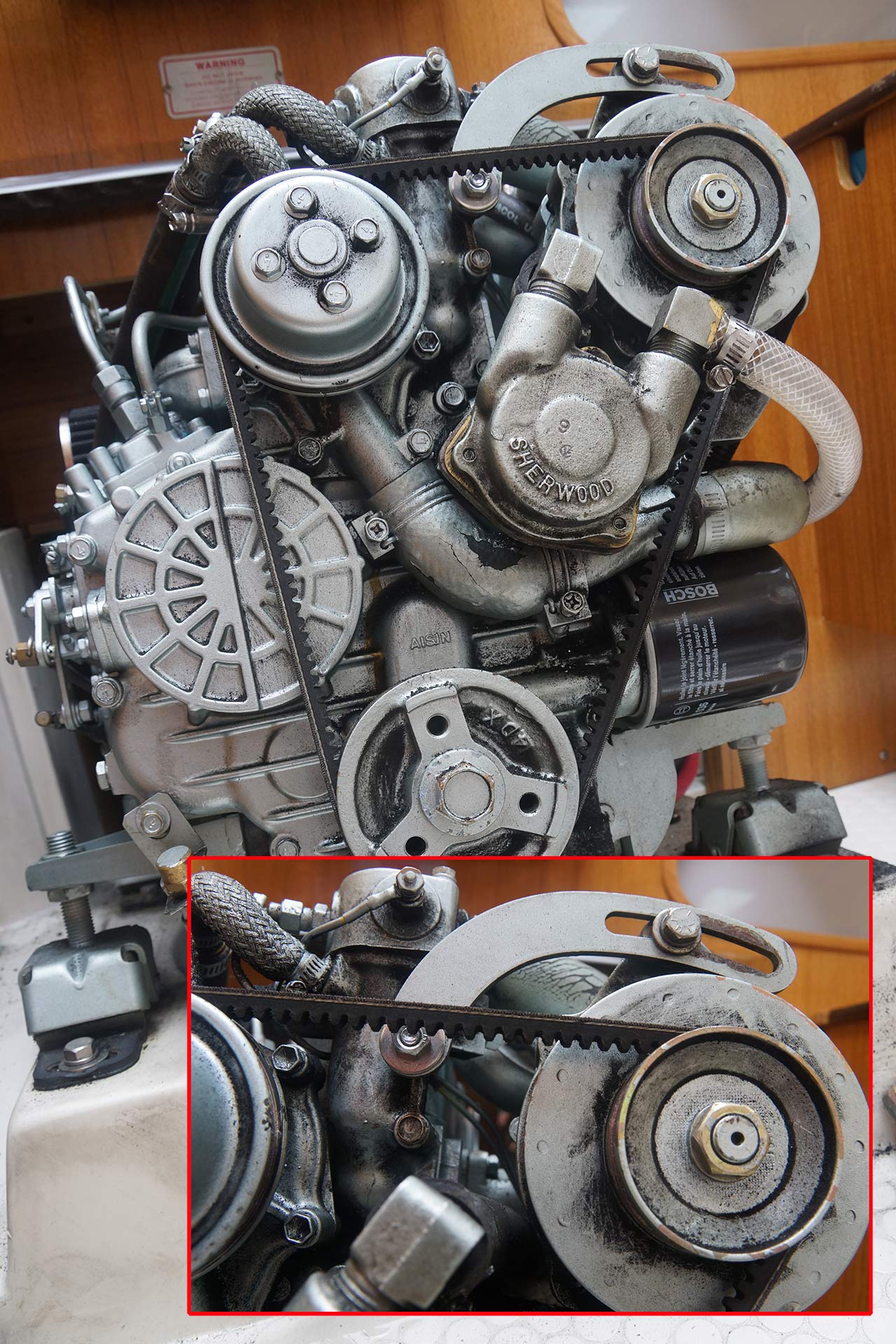
My M35B engine ALSO has only one hole in the bracket that attaches to the thermostat housing. Because I have a large aftermarket alternator, it is likely that the 2-hole design would not work. That does not allow for the bracket to pivot and therefore the curved slot has to match the exact radius of the alternator as it pivots on its lower mounting lug.
I have found that the large bolts holding bracket #17 to the lower lug of the alternator can be torqued quite high and they hold the alternator quite rigidly. I have never had a problem keeping belt tension with the upper bracket, but I agree it could be a better design.
As for the SAE (imperial) vs metric, the engine is a Kubota tractor engine made in Japan. My after-market alternator is a US product.
Duane Ising - Past Commodore (2011-2012)
s/v Diva Di
1999 Catalina 36 Hull #1777
Std rig; wing keel, M35B, Delta (45#)
Punta Gorda, FL
http://www.sailblogs.com/member/diva-di/
IMHO, the way your engine is delivered, is probably superior, and certainly more flexible, than in the diagram. As noted by Duane, the original design would not allow for installation of any alternator that didn't have the exact same radius as the original, as it couldn't pivot. I also don't think the 'pivot' bolt needs to be all that tight; the bolt that goes through the slot is the one that keeps the belt tight. The forces on the bolt holding the bracket to the engine are mainly in shear (sideways), not tension, by the bracket. Even if the bolt was not tight, the adjustment bolt through the alternator would keep tension on the belt.
I don't see anything wrong with your modification, but I wouldn't be all that concerned with how tight it holds the bracket.
Gary and Cathy Price
1997 C36 Mk II Tall Rig/Wing Keel Imagine...
Hull # 1617
Worton Creek, Md.
Northern Chesapeake Bay
Gary makes a few excellent points that I failed to mention.
Duane Ising - Past Commodore (2011-2012)
s/v Diva Di
1999 Catalina 36 Hull #1777
Std rig; wing keel, M35B, Delta (45#)
Punta Gorda, FL
http://www.sailblogs.com/member/diva-di/
Thanks for your quick responses!
Though I do agree that forces on the pivot bolt (1) are mainly sideways, it did require proper tensioning to prevent the bracket (3) from pivoting upwards around the bolt. The reason Duane hasn't got that problem, is probably due to the excellent suggestion to tension the bolts on the #17 bracket?
As I had to re-adjust the belt tension so frequently, I left those in the position where I could just pivot the alternator bolt (5) along the bracket. Never bothered with them.
Stick to the one bolt design then... Good! Saves a lot of work and Both Gary and Duane absolutely right; the two bolt fixation of bracket (3), would make replacement of the alternator by a different model very difficult!
Hadn't thought of that, till now! Thanks!
S/Y 'EASY'
C36 MkII #1739
Monnickendam -The Netherlands
www.taas.it
Here's an answer about the metric bolts although it applies to the M25-Series engine brackets.
[url]http://c34.org/bbs/index.php/topic,5078.msg47017.html#msg47017[/url]
May help out in the "logic" or lack thereof...:):(
Stu Jackson, C34IA Secretary, C34 #224, 1986, SR/FK, M25 engine, Rocna 10 (22#)
The metric/imperial thing.... Forgot to comment on that!
Stu & Duane, thanks for the back-ground info.
Nice to know I can always remodel a C36 into this...
[IMG]http://www.kubota.com/configurator/img/products/be5908c9-a7f3-4c02-90ae-...
Guess we can leave it up to the Japanese, to make a spicy mix of building codes & standards...
By the way we Dutch much prefer the metric sizes over - what the British like to call - imperial sizes.
S/Y 'EASY'
C36 MkII #1739
Monnickendam -The Netherlands
www.taas.it
If it helps to confirm - My bracket also has 1 bolt on the left side of the bracket and I have no slippage. Now that you have pointed out I too see very slight belt wear on the alternator - but I am not concerned about it. The only problem I had with the bracket was that it was hitting the water temperature alarm sender at 1200 and 200 RPM and causing the soanalert to sound in the cockpit. I paced a washer under it to pull away from the high water temperature sender and all is well.
Haro Bayandorian, 1999 C36 MKII, Sail La Vie #1787, M35B,
Coyote Point, San Mateo, CA.